“`html
The Comprehensive Guide to Aluminum plants
The Comprehensive Guide to Aluminum Plants
Aluminum, a silvery-white, lightweight, and highly versatile metal, is ubiquitous in modern life. From the cans that hold our beverages to the aircraft that traverse the skies, aluminum’s applications are vast and varied. The journey of aluminum from raw ore to finished product is a complex and energy-intensive process that occurs within specialized industrial facilities known as aluminum plants. This comprehensive guide delves into the intricate workings of these plants, exploring the processes, technologies, and environmental considerations that shape the production of this crucial material.
The Raw Material: Bauxite Ore
The story of aluminum begins with bauxite, a naturally occurring ore primarily composed of aluminum hydroxides. Bauxite deposits are found in tropical and subtropical regions around the world, with major producers including Australia, China, Guinea, and Brazil. The quality of bauxite is determined by its aluminum oxide (Al2O3) content, with higher grades yielding more aluminum. Mining operations extract bauxite through open-pit or underground methods, depending on the deposit’s location and characteristics.
Mining and Transportation
:max_bytes(150000):strip_icc()/aluminum-plant-getty-0323-2000-ff40392dd6614327982ace5579be2258.jpg)
Open-pit mining, the most common method, involves removing the overburden (soil and vegetation) to expose the bauxite ore. Heavy machinery, such as excavators and bulldozers, are used to extract the ore, which is then transported to processing facilities. Underground mining, while less common, is employed when bauxite deposits are located at greater depths. After extraction, the bauxite is typically crushed and screened to remove impurities before being transported to alumina refineries.
The Bayer Process: From Bauxite to Alumina
The Bayer process is the primary industrial method for refining bauxite into alumina (aluminum oxide). This process involves a series of chemical reactions and physical separations to isolate Al2O3 from the other components of bauxite.
Digestion
The crushed bauxite is mixed with a hot solution of sodium hydroxide (caustic soda) under high pressure. This process, known as digestion, dissolves the aluminum hydroxides in the bauxite, forming sodium aluminate. The remaining solid impurities, known as red mud, are separated from the liquid solution.
Clarification and Precipitation
The sodium aluminate solution is then clarified to remove any remaining solid particles. This is typically achieved through settling and filtration. The clarified solution is then cooled and seeded with aluminum hydroxide crystals. This initiates the precipitation of aluminum hydroxide from the solution. The precipitated aluminum hydroxide is then separated from the remaining liquid.
Calcination
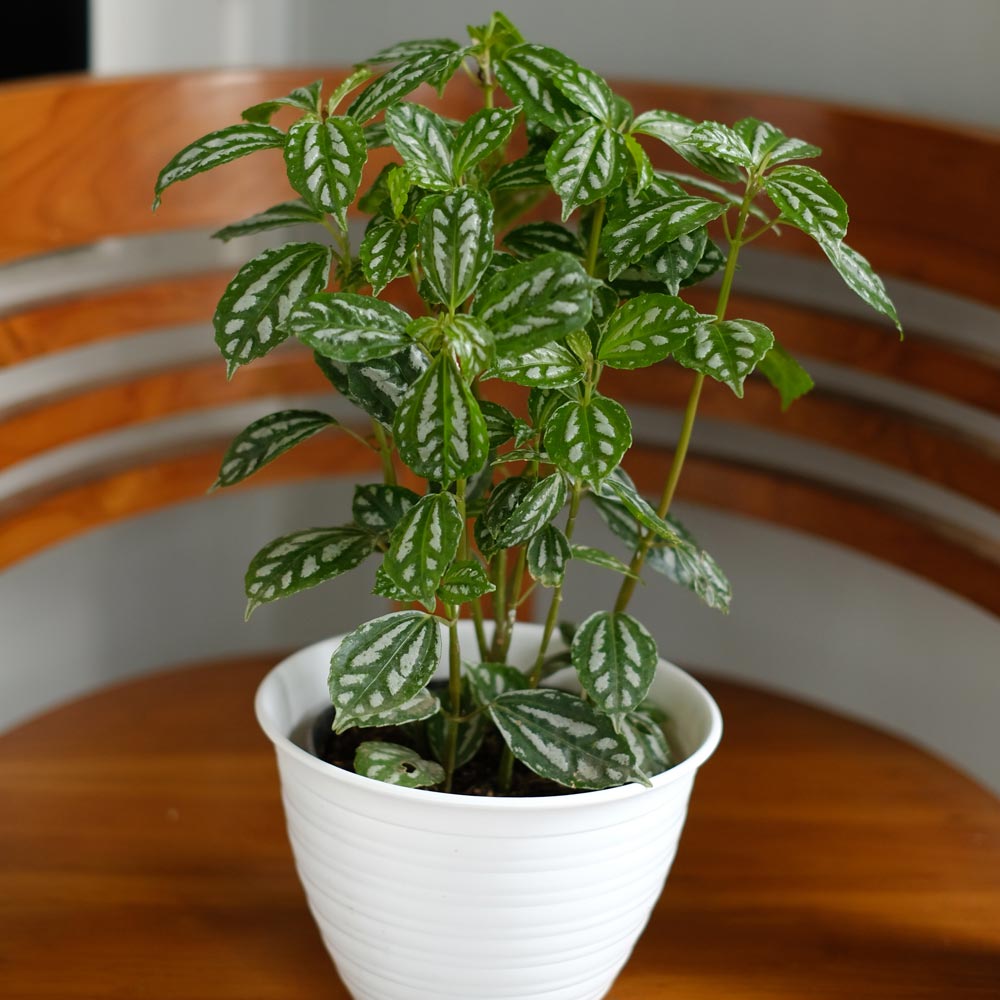
The final step in the Bayer process is calcination, where the aluminum hydroxide is heated to high temperatures (around 1000°C) in a rotary kiln. This process drives off the water molecules, leaving behind pure alumina powder. Alumina is a white, granular material that serves as the feedstock for aluminum smelting.
The Hall-Héroult Process: From Alumina to Aluminum
The Hall-Héroult process, invented independently by Charles Martin Hall and Paul Héroult in 1886, is the electrochemical method used to smelt alumina into metallic aluminum. This process involves the electrolysis of alumina dissolved in a molten cryolite bath.
Electrolysis
Alumina is dissolved in a molten cryolite bath, which acts as a solvent and reduces the melting point of alumina. The molten mixture is then placed in an electrolytic cell, also known as a reduction cell or pot. The cell consists of a carbon anode (positive electrode) and a carbon cathode (negative electrode). An electric current is passed through the cell, causing the alumina to decompose into aluminum and oxygen. The molten aluminum, being denser than the cryolite bath, sinks to the bottom of the cell, where it is periodically tapped.
Anode Consumption and Carbon Dioxide Emissions
The carbon anodes are consumed during the electrolysis process, reacting with the oxygen released from the alumina to form carbon dioxide. This results in significant carbon dioxide emissions from aluminum smelters. Efforts are underway to develop inert anodes that do not produce carbon dioxide, but these technologies are still in their early stages of development.
Casting and Fabrication
:max_bytes(150000):strip_icc()/aluminum-plant-silver-leaves-0323-2000-337f6fc734ab459b9c6cf330ef14e27e.jpg)
The molten aluminum tapped from the electrolytic cells is transported to casting facilities, where it is solidified into various forms, such as ingots, billets, and slabs. These semi-finished products are then used as feedstock for further fabrication processes.
Casting Techniques
Various casting techniques are employed to solidify molten aluminum, including direct chill casting, continuous casting, and die casting. Direct chill casting is used to produce large ingots and billets, while continuous casting is used to produce sheets and coils. Die casting is used to produce complex shapes with high precision.
Fabrication Processes
The semi-finished aluminum products are subjected to various fabrication processes to create finished products. These processes include rolling, extrusion, forging, and machining. Rolling is used to produce sheets and foils, extrusion is used to produce profiles and tubes, forging is used to produce high-strength components, and machining is used to produce precision parts.
Energy Consumption and Environmental Impact
Aluminum production is an energy-intensive process, primarily due to the high temperatures required for the Hall-Héroult process. The electricity used in aluminum smelters is typically generated from fossil fuels, contributing to greenhouse gas emissions. The industry is actively working to reduce its energy consumption and environmental impact through various initiatives.
Energy Efficiency Improvements
Aluminum producers are implementing various measures to improve energy efficiency, such as optimizing cell design, improving process control, and recovering waste heat. These measures help to reduce energy consumption and greenhouse gas emissions.
Renewable Energy Sources
Many aluminum producers are transitioning to renewable energy sources, such as hydropower, solar, and wind power. This helps to reduce the carbon footprint of aluminum production. However, the availability of renewable energy sources varies depending on location.
Recycling
Aluminum is highly recyclable, and recycling plays a crucial role in reducing the environmental impact of aluminum production. Recycling aluminum requires only 5% of the energy needed to produce primary aluminum from bauxite. Recycling also helps to reduce waste and conserve natural resources.
The Future of Aluminum Plants
The aluminum industry is undergoing a transformation, driven by the need to reduce its environmental impact and improve sustainability. Future aluminum plants are expected to incorporate advanced technologies and processes, such as inert anodes, carbon capture and storage, and closed-loop recycling. These technologies will help to reduce greenhouse gas emissions and minimize waste.
Inert Anode Technology
Inert anode technology, which replaces the consumable carbon anodes with inert materials, has the potential to eliminate carbon dioxide emissions from aluminum smelters. This technology is still in development, but it holds great promise for the future of aluminum production.
Carbon Capture and Storage
Carbon capture and storage (CCS) technology can be used to capture carbon dioxide emissions from aluminum smelters and store them underground. This technology can help to reduce greenhouse gas emissions, but it is still relatively expensive and requires further development.
Closed-Loop Recycling
Closed-loop recycling, which involves recycling aluminum scrap back into primary aluminum production, can help to reduce the need for bauxite mining and primary aluminum production. This approach can help to conserve natural resources and reduce waste.
Conclusion
Aluminum plants are essential facilities that play a crucial role in the production of this vital material. The journey of aluminum from bauxite ore to finished product is a complex and energy-intensive process, but the industry is committed to improving its sustainability and reducing its environmental impact. Through the adoption of advanced technologies and processes, the aluminum industry is working towards a more sustainable future.
“`